by
[user not found]
| Nov 20, 2015
Kaizen is most commonly associated with Lean manufacturing and has since expanded to other industries including education, leadership and many more in recent years.
But potholes, road work and city management operations?
One city in Iowa figured out a way to apply Lean thinking to pothole repair and lay the foundation for a sustainable, efficient solution to fixing the city’s pothole repair and response time.
The city of Fort Dodge, Iowa recently conducted a kaizen on the city’s pothole patching efforts. Naturally, once the kaizen was completed, the city manager and his staff found that there were many opportunities to improve a process that often goes overlooked. The final report and synopsis found that some areas from a resident education standpoint and others from a process oriented.
At this past Iowa Lean Consortium, the city manager of Fort Dodge met up with our management team from VIBCO at the event and eagerly shared with us their presentation, data and findings for this particular series of improvements.
Here’s how Fort Dodge, Iowa worked to solve their pothole problem with Kaizen and Lean ideas.
Kaizen and Pothole Repair: Finding What Needs to Be Changed
The Fort Dodge city manager and his team developed two objectives. Each objective was aimed at improving the pothole repair process from the resident’s end all the way through to the team tasked with fixing the pothole. The first was to develop a process which potholes can be patched in 24 hours of the citizen reporting it. The second goal was to provide a simple and effective way to track the progress of their pothole repair statuses.
Both issues are things that citizens in all towns and cities across the country grapple with and both, as it turns out, can be solved. The team concluded that the voice of the customer (or resident in this case) broke down as follows:
- Get the potholes filled quickly
- Make the potholes durable and lasting
- Minimize the traffic disruptions in the process of repair
- Make pothole repair easy to report
With regards to the city employee:
- They must remain safe during the repair process
- Make reporting potholes easy for residents
- Make it easy for citizens to track the status of pothole repair
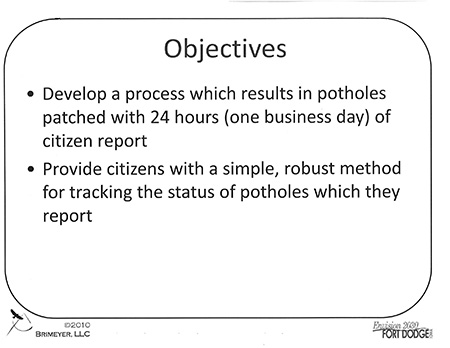
Identifying Waste in the Process of Pothole Repair
There is waste in everything if you look hard enough and pothole repair is no exception.
What the city of Fort Dodge found was that, concerning waste, there are things that can be fixed within 5 of the 7 major wastes.
In processing, the team found that cold patch mix exposed to the elements requires a lot of extra work to make it easy for road repair teams to move out of the truck and to the hole. Defects in the process include the wrong location of the potholes and incorrect information initially. Transportation waste, the waste incurred from the movement of resources from one place to another, means that it often takes teams longer to get to the pothole site then to repair the pothole. Information processing, a subdivision of processing as a whole, meant that the information chain of how the city finds out about a pothole was lengthy and convoluted with many places for information to get lost or misunderstood.
Motion waste, waste caused by the physical movement of completing a process, was the largest area of waste. Wasted motion in the pothole repair process included:
- Setting the delineators
- Cleaning the pothole
- Adding material to the pothole
- Tamping the material down
- And picking up the delineators
Current State and Future State
Mapped out, here is the current state of the pothole repair process:
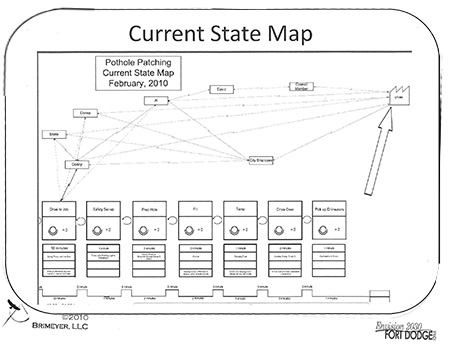
Here is the future state map the city developed:
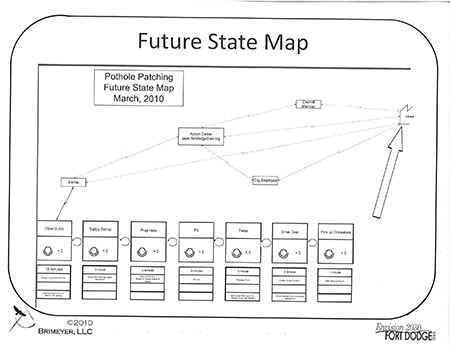
Breakthroughs and Developments
With any kaizen, there are breakthroughs and revelations about the process and what can be changed for the better. Among the city’s changes and breakthroughs were:
- Implementing an Action center for pothole reports
- Having pothole repair teams flex based on demand and
- Protection UPM from elements to achieve a quality, lasting patch
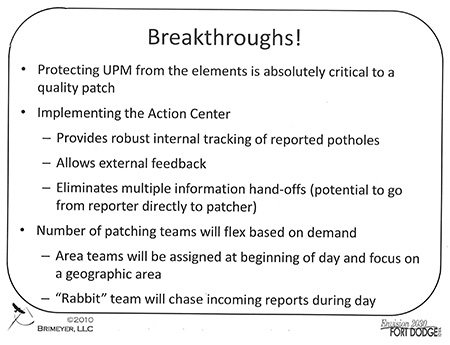
Additional Improvements and Changes, Action Plan
Not only did this kaizen help to achieve the two major objectives for the city’s pothole repair efforts, but many other improvements came about as well. Some of the improvements include:
- An email published to all Fort Dodge employees encouraging them to report potholes and take input calls from citizens directly to the newly minted Action Center
- An article written and submitted to The Messenger, a news publication covering the Fort Dodge area introducing

Metrics and Success Measurement
The city manager and team decided that success would be measured by the following parameters:
- The number of potholes patched
- Response time from report to completed state
- And percentage of potholes patched within 24 hours
Wrap Up
New applications of Lean principles are always exciting to hear about and this one is no exception. It's no secret that we at VIBCO have been very active in Rhode Island's pothole hole repair efforts so to learn about another organization and group tackling potholes in a different way is phenomenally exciting to hear about. We're extremely grateful that the city manager of Fort Dodge shared his experience with us and we're very excited to share it with everyone.